Highlights include
The Problem
An international auto parts manufacturer and distributor was facing multiple operational challenges that severely impacted their productivity and cost efficiency:
- Service Level Challenges: Struggled consistently to meet service level targets, considering nearshoring production due to inefficiencies.
- Operational Downtime: Frequent and significant periods of downtime due to equipment and process issues.
- Workforce Issues: High levels of absenteeism, lack of accountability from staffing partners, and employee fatigue due to rigorous overtime schedules.
- Quality and Re-work: Persistent quality issues led to substantial re-work, impacting overall productivity.
- Process Flow Inefficiencies: Insufficient process documentation, heavy reliance on tribal knowledge, and lack of a succession plan in key roles.
- Weekend Shift Productivity: Lower output and higher costs on weekends due to inadequate staffing and preparation.
Our Plan
To address these challenges, iJility implemented a strategic, phased approach:
Phase 1: Workforce Stabilization
- On-site Leadership Deployment: Engaged iJility’s Implementation, Leadership, and Engineering teams on-site to provide immediate oversight and direction.
- High-Performance Teams: Assigned dedicated high-performance work teams to stabilize the weekend shift, followed by weekday shift optimization.
- Performance Monitoring: Implemented continuous performance monitoring and feedback loops to ensure accountability and improvement.
Phase 2: Operational Enhancements
- Quality and Tracking Improvements: Enhanced quality audit programs and introduced advanced tracking tools, including a new site dashboard for real-time client visibility.
- Training and Skill Development: Developed refined training materials, introduced cross-training programs, and reduced learning curves for new employees.
- Digital and Data Tools: Deployed digital downtime tracking tools and a line changeover rate tracker to analyze and continuously improve operational efficiency.
- Labor Optimization: Streamlined labor management by converting contingent labor to iJility payroll and optimizing labor cost per unit through a Cost Per Unit (CPU) pricing model.
Our Execution
iJility swiftly executed these strategies to optimize the client’s operations:
- Onboarding and Training: Successfully onboarded new staff and leadership, significantly improving workforce readiness and flexibility.
- Process Improvements: Reworked the intake process, reduced dock-to-stock times, relocated returns operations to an external facility, and initiated SKU consolidation efforts.
- Continuous Improvement: Implemented a robust process integrity program, standardized workflows, and enhanced communication between departments to sustain operational improvements.
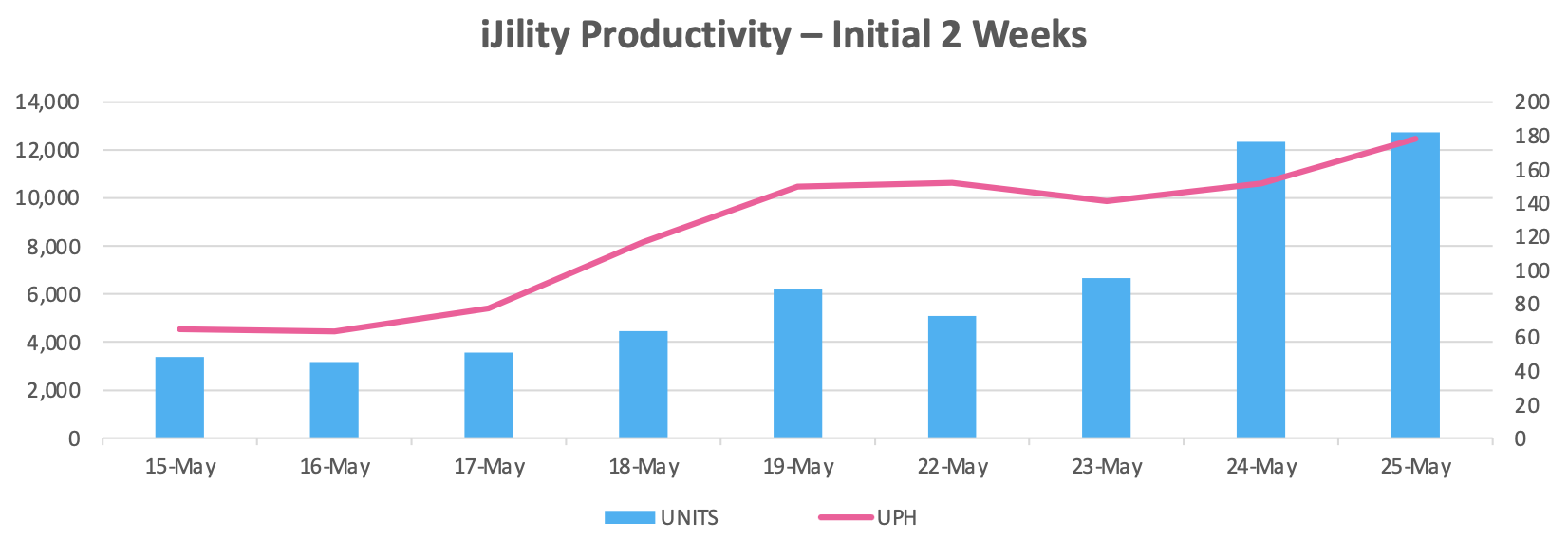
The Results
iJility’s focused approach delivered exceptional results for the client:
- Record Output Levels: Achieved record output levels in the initially occupied work cell, clearing a significant backlog within two weeks.
- Efficiency Improvements: UPH increased by 16.3%, with daily production volumes rising by 100.5%.
- Cost Reductions: Labor cost per order reduced from $11.79 to $4.98 over three years, with a 54% reduction in the per-unit cost in the new business vertical.
- Operational Optimization: Successfully transitioned 150+ positions to iJility payroll within a week and reduced overall operational downtime through improved scheduling and process management.
- Sustained Performance Gains: Continuous efficiency improvements week over week, leading to strategic decision-making and long-term sustainability.
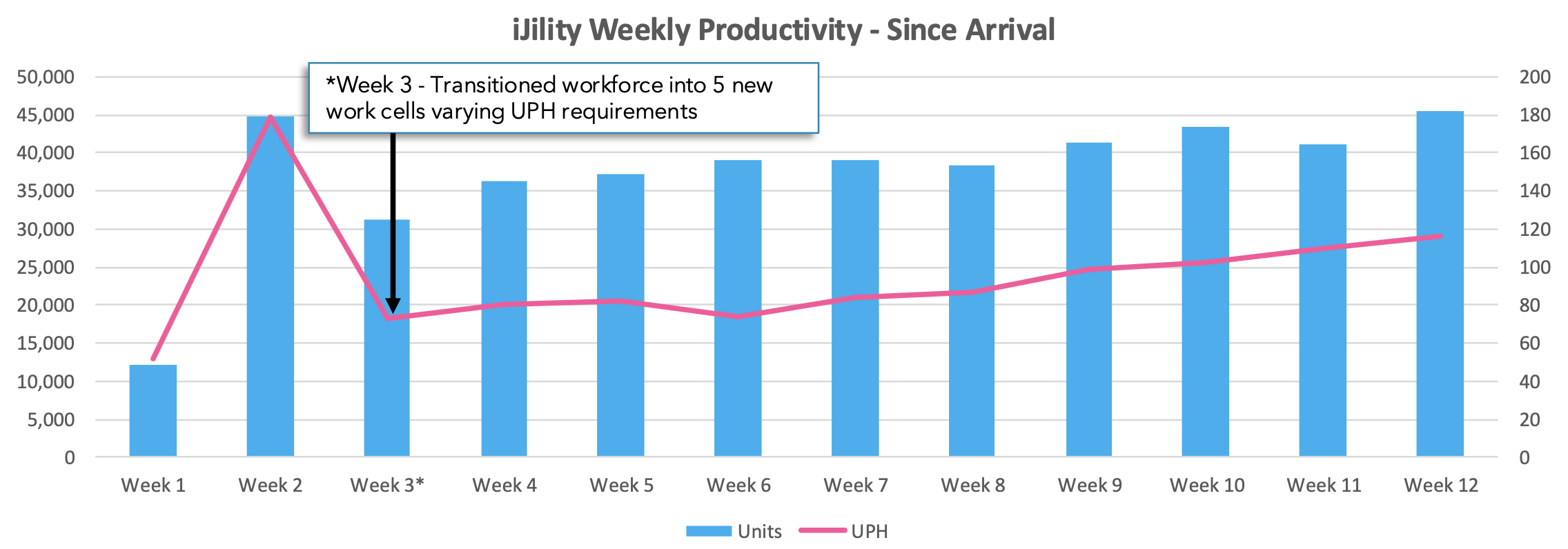
Let Us Help
Are you facing similar challenges in your operations? iJility specializes in delivering tailored workforce solutions that drive productivity and efficiency. Let us partner with you to transform your workforce and achieve your operational goals.
Innovative – Strategic – Accountable