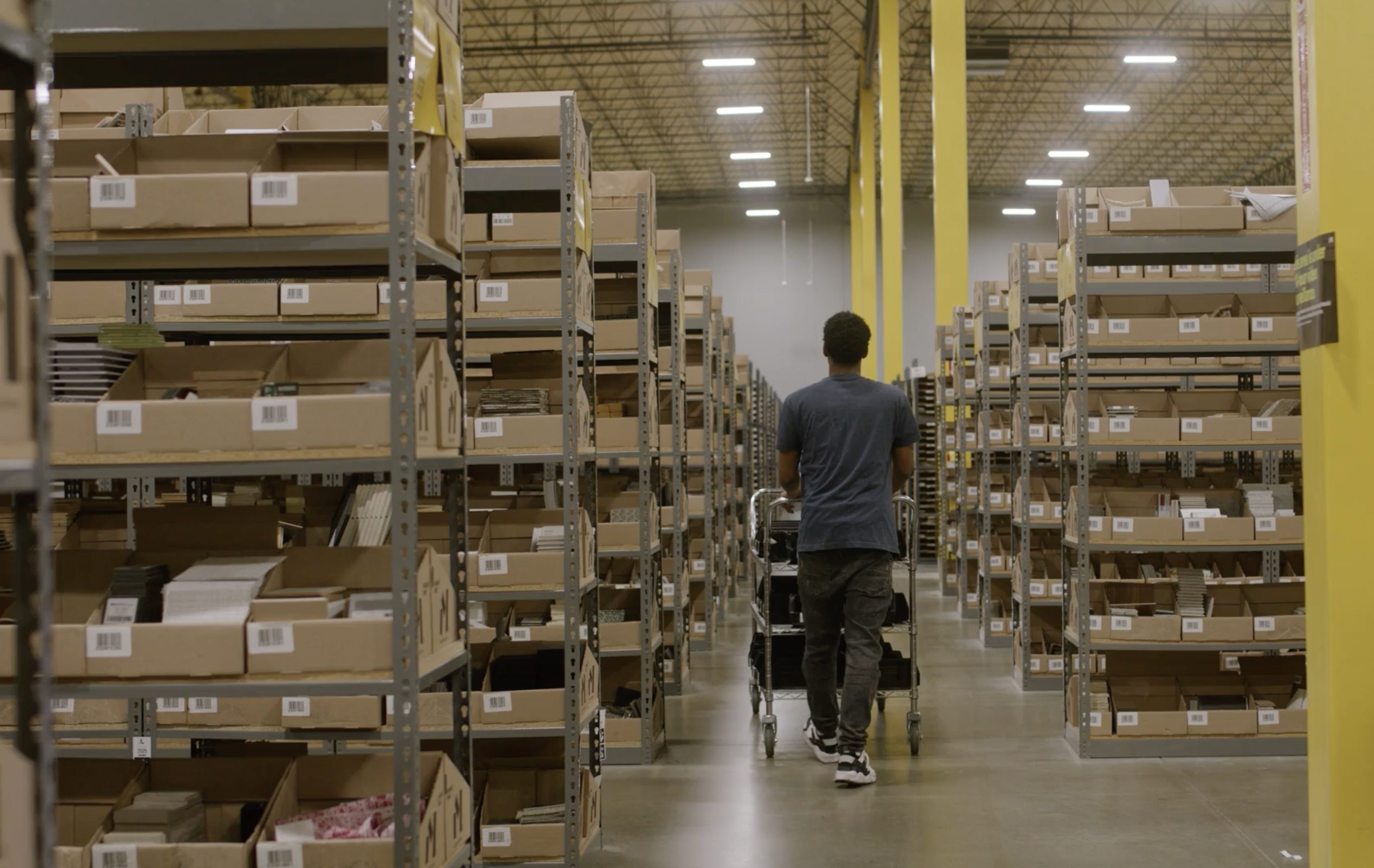
With rising labor costs impacting the bottom line of many businesses, finding effective ways to cut labor costs in fulfillment centers has become a top priority. By leveraging proven strategies and embracing technological advancements, companies can significantly improve their operational efficiency and financial performance. Key strategies include improving labor forecasting, optimizing scheduling processes, investing in employee training and development, and adopting advanced technologies. This article delves into the first of these strategies — improving labor forecasting and scheduling optimization — to provide concrete steps that businesses can take to efficiently manage their workforce and reduce labor costs.
Improving Labor Forecasting and Scheduling Optimization
One of the most effective ways to cut labor costs in fulfillment centers is to improve labor forecasting. Leveraging historical workload patterns and visibility into upcoming orders can help companies accurately predict staffing needs before work schedules are published. By analyzing past data on order volumes, peak periods, and seasonal fluctuations, fulfillment centers can create more precise labor forecasts. Integrating real-time data on incoming orders further refines these predictions, leading to more efficient staffing and reduced labor costs.
Another key strategy is to implement advanced workforce scheduling software. These systems should consider various worker attributes such as skills, certifications, preferences, and availability in order to optimize scheduling. Real-time visibility across all labor pool resources enables managers to make informed decisions and quickly adapt to changing demands. This not only ensures optimal staffing levels but also reduces the need for last-minute adjustments that can lead to overtime costs.
Finally, automating scheduling processes can proactively respond to situations like covering open shifts while considering critical factors such as compliance and overtime. Automated systems can rapidly identify the most suitable employees to fill open shifts based on predefined criteria. This ensures compliance with labor regulations, minimizes overtime costs, and maintains optimal staffing levels. Through this proactive approach, companies can effectively manage their workforce, reduce labor costs, and improve operational efficiency.
Investing in Employee Training and Development
Another proven method to cut labor costs in fulfillment centers effectively is investing in comprehensive onboarding and ongoing training programs. A well-trained workforce is more than just an expense — it’s an investment that pays off in numerous ways. When employees have the necessary skills and knowledge to perform their roles effectively, they are more productive, make fewer errors, and adapt better to new technologies and processes. This investment in training reduces the learning curve for new hires and minimizes the time and resources spent on correcting mistakes or inefficiencies. Not only does it result in immediate cost savings, but it also drives long-term productivity improvements.
Cross-training initiatives are another effective way to reduce labor costs. By training employees in multiple roles and functions, fulfillment centers can create a more versatile and flexible workforce. With a cross-trained staff, you can easily redeploy resources to areas with higher labor demands, adapting to fluctuating needs without incurring additional labor costs. Moreover, cross-training promotes employee engagement and job satisfaction, as it provides opportunities for growth and development. An engaged and satisfied workforce is more productive, less likely to leave, and therefore, less costly to replace — further reducing labor costs.
Establishing clear performance standards and providing regular feedback and coaching is another critical component of effective labor cost management. With well-defined performance expectations in place, employees can understand their strengths and areas for improvement. Regular coaching sessions foster a culture of continuous learning and development, leading to a more skilled and efficient workforce. This approach not only improves productivity but also enables employees to take ownership of their performance, reducing the need for managerial intervention and thus further cutting labor costs.
Optimizing Existing Labor, Technologies, and Workflows
Effectively reducing labor costs in fulfillment centers requires a strategic approach to the optimization of existing resources. By conducting a thorough assessment of your current staff performance, skills, and utilization, you can identify opportunities for productivity enhancement. This analysis could involve reorganizing teams, reassigning tasks, or even eliminating redundant roles to streamline operations and reduce labor costs. By optimizing your existing workforce, you can ensure that each employee is in a role that best utilizes their skills and contributes to efficient operations.
Equally crucial is the evaluation and optimization of existing technologies in the fulfillment center. Automated systems such as Pick-to-Light, Pick-to-Voice, or Augmented Vision can significantly enhance productivity when used to their full potential. Regular assessments of these technologies ensure their optimal performance and provide opportunities for fine-tuning.
Fulfillment centers must also examine their current processes and workflows to identify and eliminate bottlenecks or inefficiencies contributing to increased labor costs. By conducting a detailed analysis of each step in the fulfillment process, from receiving and putaway to picking, packing, and shipping, you can identify areas for improvement. Streamlining workflows involves eliminating unnecessary steps, minimizing travel time, and improving the overall flow of goods and information. These actions result in a more efficient process, saving time, reducing waste, and effectively cutting labor costs.
Through careful analysis and optimization of existing labor, technologies, and workflows, fulfillment centers can implement effective strategies to cut labor costs. By focusing on these key areas, you can create a leaner, more efficient operation that not only saves money but also enhances overall productivity and service delivery.
Implementing Advanced Technologies for Labor Optimization
Adopting advanced technologies can significantly improve efficiency and provide effective ways to cut labor costs in fulfillment centers. One such technology is a high-quality Warehouse Execution System (WES). A WES optimizes labor and equipment utilization across the entire facility by dynamically allocating resources, balancing workloads, and coordinating activities between humans and machines. Leveraging real-time data and intelligent algorithms, a WES ensures tasks are assigned to the right resources at the right time, minimizing idle time and maximizing productivity.
Another groundbreaking technology that can help reduce labor needs is Autonomous Mobile Robots (AMRs). AMRs navigate the warehouse floor independently, assisting with tasks such as transporting goods, picking items, or conducting inventory counts. By working alongside human employees, AMRs streamline processes and reduce the physical demands on the workforce. This allows staff to focus on higher-value tasks while the robots handle repetitive and time-consuming activities.
Automated Storage and Retrieval Systems (AS/RS) are also instrumental in the automation of processes that would typically require human workers. AS/RS can store and retrieve items quickly and accurately, reducing the need for manual labor in putaway and picking operations. When combined with robotic picking arms, AS/RS can enable a fully automated picking process, significantly reducing labor requirements in the most labor-intensive areas of the fulfillment center.
The Final Takeaway
Optimizing existing labor, technologies, and workflows, combined with the implementation of advanced technologies, are effective ways to cut labor costs in fulfillment centers. By investing in a high-quality Warehouse Execution System (WES) and deploying Autonomous Mobile Robots (AMRs), you can optimize labor and equipment utilization, streamline processes, and reduce physical demands on the workforce. Moreover, implementing Automated Storage and Retrieval Systems (AS/RS) can automate processes, further reducing labor requirements.
Given these advancements, how prepared is your fulfillment center to embrace these technological solutions for labor optimization? Are you ready to transition towards a more efficient, cost-effective operation?
If you’re ready to take your operation to the next level, schedule a discovery call with us at iJility. We’re here to help you achieve your full potential.